Florida Footing Vapor Barriers: What You MUST Know!
The Florida Building Code (FBC), a regulatory framework impacting construction standards statewide, specifically addresses requirements related to foundation integrity. These regulations often necessitate the implementation of a florida building code footing vapor barrier. Vapor permeance, a crucial material property, dictates the rate at which moisture passes through a vapor barrier. Properly installed vapor barriers can increase the value and longevity of your property and home by protecting the concrete in the foundation and reducing the risk of damage.
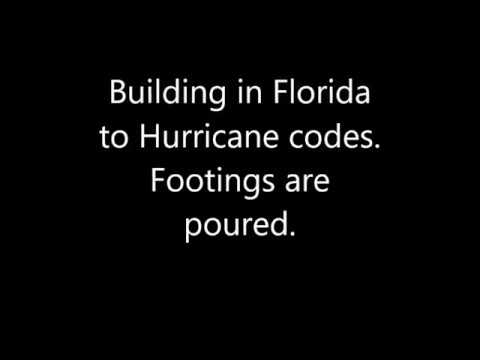
Image taken from the YouTube channel Mighty House , from the video titled Building in Florida to Hurricane codes, Footings are poured!! .
Florida Footing Vapor Barriers: What You MUST Know!
This guide provides a comprehensive overview of footing vapor barriers in Florida, specifically addressing the requirements outlined in the florida building code footing vapor barrier regulations. It aims to clarify the purpose, implementation, and importance of these barriers in protecting structures in Florida's unique climate.
Understanding Footing Vapor Barriers
Footing vapor barriers are materials installed between the concrete footing and the soil to prevent moisture from migrating upwards into the foundation and subsequently, the building structure. In Florida, where high humidity and water tables are prevalent, these barriers are crucial for maintaining structural integrity and preventing moisture-related problems.
Why are Vapor Barriers Necessary in Florida?
-
High Humidity: Florida's consistently high humidity levels create a significant vapor pressure difference between the soil and the interior of buildings. This pressure drives moisture upwards through porous materials like concrete.
-
High Water Tables: Many areas in Florida have elevated water tables, increasing the risk of water penetration into the foundation.
-
Soil Composition: The composition of Florida soils, often sandy and porous, allows for easy movement of water vapor.
-
Protection Against Moisture-Related Problems: Preventing moisture ingress helps mitigate:
- Mold and mildew growth
- Wood rot
- Corrosion of metal components
- Compromised indoor air quality
Florida Building Code Requirements for Footing Vapor Barriers
The florida building code footing vapor barrier specifications are designed to ensure adequate protection against moisture intrusion. Specific sections of the code address vapor barrier requirements. While the exact code section numbers may vary based on the edition of the code, the core requirements generally remain consistent. Always consult the most recent version of the Florida Building Code for the most accurate and up-to-date information.
Key Code Provisions
-
Material Specifications: The code often specifies the type of material required for vapor barriers. Commonly, this includes polyethylene sheeting of a certain thickness (measured in mils). This thickness is crucial for providing adequate resistance to vapor transmission.
- Example: The code may specify a minimum of 6-mil polyethylene sheeting.
-
Installation Requirements: The method of installation is also regulated. Proper overlap of the vapor barrier sheets and sealing of seams are critical to prevent moisture from bypassing the barrier.
- Minimum overlap distances are typically specified (e.g., 6 inches or more).
- Sealing may be required at penetrations, such as pipes or electrical conduits.
-
Placement: The vapor barrier must be placed directly between the concrete footing and the underlying soil. This placement ensures continuous coverage and prevents moisture from contacting the concrete.
Variations and Exemptions
-
Soil Conditions: In some instances, the code may allow for variations based on site-specific soil conditions. A geotechnical report may be required to justify any deviations from the standard requirements.
-
Engineered Systems: Alternatively, engineered systems that achieve equivalent or superior moisture protection may be approved by the building official.
Selecting the Right Vapor Barrier Material
Choosing the appropriate vapor barrier material is essential for long-term performance. Considerations include:
-
Perm Rating: The permeance rating of the material indicates its ability to resist water vapor transmission. Lower perm ratings indicate better resistance.
-
Durability: The material should be durable enough to withstand installation stresses and resist degradation over time.
-
Resistance to Punctures: During installation, the vapor barrier must be resistant to punctures from sharp objects or rough surfaces.
-
Compatibility: The material should be compatible with the concrete and any other materials used in the foundation system.
Common Vapor Barrier Materials
Material | Description | Advantages | Disadvantages |
---|---|---|---|
Polyethylene Sheeting | A plastic film commonly used for vapor barriers, available in various thicknesses. | Cost-effective, readily available, easy to install. | Can be punctured easily if not handled carefully, may degrade over time if exposed to UV radiation. |
Reinforced Polyethylene | Polyethylene sheeting reinforced with fibers for increased strength and durability. | Greater tear resistance and puncture resistance compared to standard polyethylene. | More expensive than standard polyethylene. |
Specialty Membranes | Engineered membranes with specific properties for vapor and water protection. | Superior performance, enhanced durability, may offer additional benefits (e.g., radon resistance). | More expensive than polyethylene options, may require specialized installation techniques. |
Proper Installation Techniques
Correct installation is just as important as selecting the right material. Poor installation can compromise the effectiveness of the vapor barrier, regardless of its quality.
- Surface Preparation: Ensure the soil surface is smooth and free of sharp objects that could puncture the vapor barrier.
- Overlap Seams: Overlap seams by the minimum amount specified in the building code.
- Seal Seams: Use appropriate tape or sealant to create a continuous, airtight barrier at seams.
- Seal Penetrations: Carefully seal around any penetrations, such as pipes or electrical conduits.
- Secure the Barrier: Secure the vapor barrier in place to prevent it from shifting during concrete pouring.
- Inspect for Damage: Before pouring concrete, thoroughly inspect the vapor barrier for any punctures or tears and repair them immediately.
Inspection and Maintenance
Regular inspection of the foundation can help identify potential moisture problems early on. Addressing these issues promptly can prevent more significant damage down the road. While the vapor barrier itself is not directly visible after construction, signs of moisture intrusion in the basement or crawl space may indicate a problem with the vapor barrier or other aspects of the foundation system.